بالا و پایین یک محصول کوچک معدنی
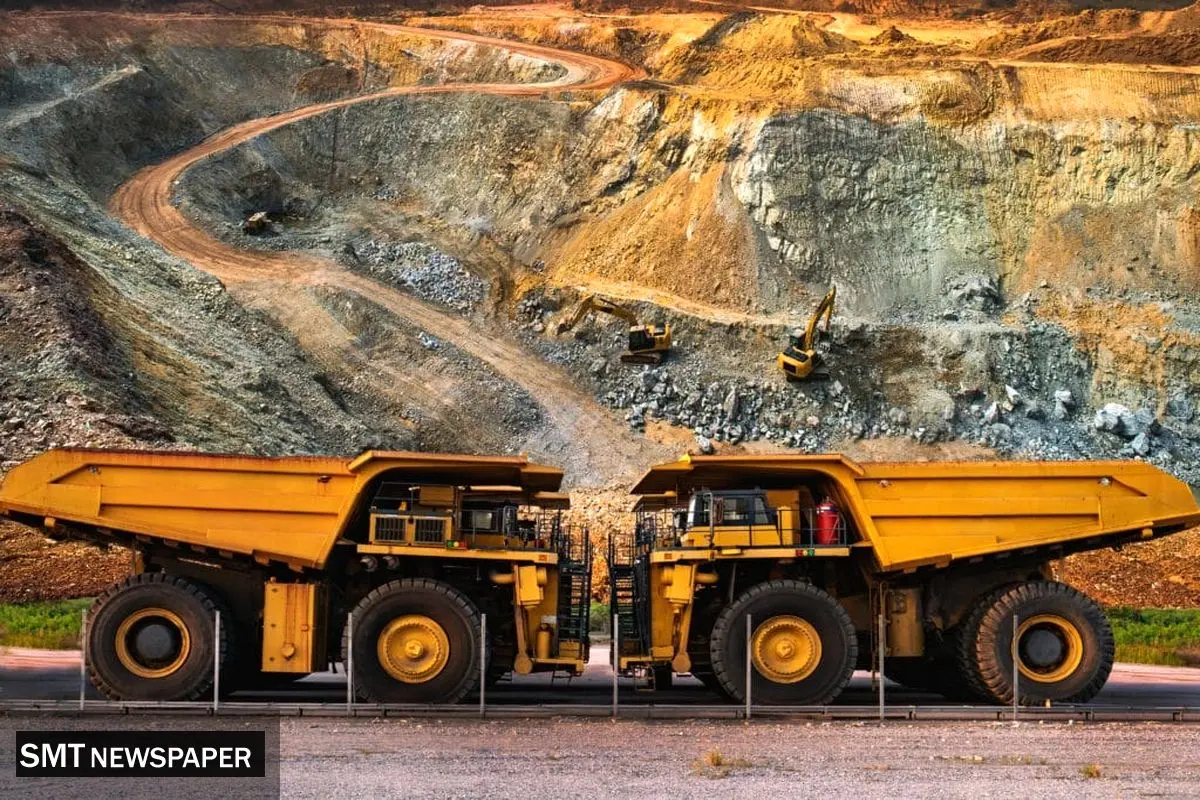
آهناسفنجی در ساخت محصولات فولادی مثل شمشفولادی، استفاده در کوره قوسالکتریکی یا کوره القایی، چدنسازی، اسلحهسازی و ابزارسازی است. بهدلیل بالا بودن درصد خلوص، آهناسفنجی در صنایع نامبرده، کاربرد زیادی دارد، زیرا در نهایت محصول فولادی استحکام بیشتری دارد. بیشتر کارخانهها آهناسفنجی ساختهشده را در بخشهای دیگر مورداستفاده قرار میدهند، اما بعضی دیگر از کارخانهها، آهناسفنجی را بهفروش میرسانند. همچنین شاید جالب باشد که بدانید ۵ درصد از آهن تولیدشده در دنیا به روش احیای مستقیم تولید میشود. آهناسفنجی هم مانند دیگر محصولات فولادی علاوه بر مزایایی که دارد، معایبی هم دارد. از مزایای آهناسفنجی، میتوان به درصد خلوص بالای آهن اشاره کرد. از سوی دیگر، وجود چند روش مختلف تولید آهناسفنجی منجر به ایجاد اندکی تفاوت در ترکیب شیمیایی محصول نهایی میشود، زیرا تمام سنگآهنها با دمای یکسان ذوب نمیشوند.
تاریخچه و تعریف آهناسفنجی
آهناسفنجی یک فرآیند تولید آهن است که از اکسایش یعنی کاهش مستقیم سنگآهن به آهن توسط گاز احیایی یا کربن تولید میشود. این فرآیند به فرآیندهای حالت جامد اشاره دارد که اکسیدهای آهن را به آهن فلزی در دمای زیر نقطهذوب آهن کاهش میدهد. احیای آهن مستقیم نقش بسیار مهمی در تولید فولاد و آهن دارد و باعث صرفهجویی در انرژی و کاهش هزینههای تولید محصولات فلزی میشود. روشهای احیای مستقیم سنگآهن، به 2 دسته پایه گاز و پایه زغالسنگ تقسیم میشوند که هدف آنها، بیرون راندن اکسیژن موجود در اشکال مختلف سنگآهن و تبدیل آن به آهن فلزی است. این فرآیند نسبتا کارآمد است و در صنعت مدرن بهخوبی توسعه یافته است. آهناسفنجی بهوسیله احیای مستقیم تولید میشود و باعث ایجاد فولادهای تخصصی با میزان کمتری ناخالصی و کارآیی بالاتر در مقایسه با روشهای سنتی تولید فولاد میشود.
فرآیند تولید آهناسفنجی یک فرآیند حیاتی در صنعت فولادسازی است که با استفاده از کورههای القایی بهانجام میرسد. این فرآیند شامل مراحل مختلفی از جمله احیای مستقیم گندله سنگآهن و تبدیل آن به آهناسفنجی، ریختهگری و تولید محصولات نهایی مانند میلگرد میشود. مزایای این روش شامل خلوص و کیفیت بالا، قابلیت تبدیل به فولاد با خواص موردنظر و استفاده گسترده در صنایع مختلف است. استفاده از کورههای القایی برای تولید آهناسفنجی دارای مزایا و معایب خاصی است. از یکسو، این روش توانایی تولید آهناسفنجی با خلوص و کیفیت بالا را دارد و قابلیت تبدیل شدن به محصولات فولادی مختلف را فراهم میکند. از سوی دیگر، ممکن است برخی روشهای تولید مختلف، بهرهوری و بازدهی بالاتری داشته باشند. فرآیند تولید آهناسفنجی از احیای مستقیم گندله سنگآهن شروع شده و با تبدیل آن به آهن احیای مستقیم ادامه مییابد. سپس بهصورت ریختهگری در ظروف خاص قرار میگیرد و به محصولات نهایی مانند میلگرد تبدیل میشود.
کمبود ضایعات آهن و افزایش نرخ آن
مهرداد اکبریان، رئیس انجمن سنگآهن ایران در ارتباط با وضعیت استفاده از آهناسفنجی و فرآیند تولید آن به صمت گفت: یکی از دلایل رواج استفاده از آهناسفنجی، کمبود ضایعات آهن و افزایش نرخ آن و مشکلات زیستمحیطی است. آهناسفنجی پس از ذوب و احیا در فولادسازی، در فرآیند ریختهگری بهشکل محصولات موردنیاز در میآید و به ۳ شکل اسلب (تختال)، بیلت (شمش) و میلگرد مورداستفاده قرار میگیرد. آهناسفنجی، محصول احیای مستقیم سنگآهن (گندله) در عملیات احیای مستقیم است که بدوننیاز به ذوب سنگآهن و با حذف اکسیژن ایجاد میشود. شکل ظاهری آن بهصورت قطعات کروی (گندله) یا اسفنجگونه بوده که دلیل نامگذاری آن هم، همین ظاهر اسفنجی این محصول است. ایران و هند بزرگترین تولیدکنندگان آهناسفنجی در جهان هستند.
اکبریان ادامه داد: عمدهکاری که در بخش فولاد تا به حال انجام شده، در بخش کوره بلند بوده است که در این روش که از ۵۰ سال و قبلتر از آن انجام میشده، سنگآهن را بهصورت مستقیم احیا میکردهاند. بعد از آن روشهای جدیدی بهکار گرفته شد که از آن جمله میتوان به «میدرکس» و «القایی» اشاره کرد که بحث آهناسفنجی در آن زمان مطرح شد و در این فرآیند، سنگآهن به کنسانتره و بعد از آن به گندله تبدیل و گندله تبدیل به آهناسفنجی میشد، این روش مزیتهایی را نسبت به روش قبل از آن دارا بود که از آن جمله میتوان به گستردگی دامنه استفاده از مواد معدنی اشاره کرد، چون بالاخره مستقیم استفاده نمیشد و در فرآیند کنسانترهسازی، سنگهای عیار پایین را استفاده و عیارسازی کرده و بهصورت همگن استفاده میشد. این موضوع باعث شد معادن بیشتری در این فرآیند فعال شوند و دامنه موادی که تامینکننده مواد خام این صنعت بودند، بیشتر شود.
برهه مرحله معدن تا آهناسفنجی
وی گفت: در واقع این فرآیند پس از تبدیل به آهناسفنجی از سوی کارخانهها مورد بررسی قرار میگیرد، چراکه هم سرمایهگذاری خیلی کلانی میخواهد تا آهناسفنجی تبدیل به شمش شود و هم اینکه ارزشافزودهای که در این فرآیند محاسبه میشود، نسبت به این حجم از سرمایهگذاری سود بالایی ندارد. از همینرو بود که بسیاری از کارشناسان در سالهای گذشته مطرح میکردند که ایران در این برهه، مرحله معدن تا آهناسفنجی را با قدرت طی کند، اما مراحل بعد از آهناسفنجی را نسبت به نیاز داخلش در نظر گرفته و بهکار بگیرد، حتی پیشنهاد این بود که آن ۸ طرح فولادی که از زمان دولت نهم شروع شدند و به نتیجه نرسیدند، تا مرحله آهناسفنجی باشند.
اکبریان در پاسخ به این سوال که مزیت و فایده استفاده از آهناسفنجی چیست، گفت: در داخل کشور میتوان کارخانهها و صنایعی را ایجاد کرد که آهناسفنجی را دریافت کرده و شمش تحویل دهند؛ از اینرو با یک سیستم بسیار ساده، میتوان کورههای ذوب ضایعات آهنی را با یک تغییر جزئی بهسمتی هدایت کرد که بتوانند از آهناسفنجی هم استفاده کنند. در واقع با این روند میتوان ترکیه را که یکی از بزرگترین مصرفکنندههای همسایه ایران است و آهناسفنجی میتواند مقصد بسیار خوبی برای این کشور باشد، بهسمت خرید این محصول از ایران سوق داد تا در کورههای ذوب ضایعاتی در آن کشور با یک تغییر جزئی از این محصول استفاده شود. از سوی دیگر، کشورهای عربی که عمدتا مواد معدنی ندارند، میتوانند از آهناسفنجی استفاده کنند. در اینباره یکی از مشکلاتی که آهناسفنجی دارد، این است که بهدلیل اشتعالزایی که دارد و حمل آن کار بسیار سختی است، حملونقل آن مشکل است. یک مرحله دیگر بعد از آهناسفنجی، بحث «بریکت» است، در واقع باید آهناسفنجی را تبدیل به بریکت که همان آهناسفنجی فشرده است، کرد که خاصیت اشتعالزایی را هم تحتتاثیر قرار داده و از بین میبرد. در واقع زمانی که تبدیل به بریکت میشود، حملونقل آن آسانتر انجام میشود، هم در داخل کشور و در مسافتهای طولانی میتوان آن را جابهجا کرد و هم در صادرات آن میتوان بهراحتی عمل کرد.
کشورهای عربی، قطر و ترکیه؛ مشتریان آهناسفنجی خواهند بود
اکبریان در ادامه این گفتوگو خاطرنشان کرد: کشورهای عربی، قطر و ترکیه مشتریان آهناسفنجی خواهند بود. از فرآیند آهناسفنجی در هر جایی نمیتوان استفاده کرد، در واقع به این دلیل که ایران شرایط خاصی در منطقه دارد، میتواند در مسیر تولید و صادرات آهناسفنجی اقدامات مهمی را در پیش بگیرد. شنیده میشود که هند هم در این زمینه، حتی بیشتر از ایران در حال کار کردن است و باید از این محصول بهعنوان یک مزیت برای کشور استفاده کرد. همسایههای ایران را میتوان ظرفیتهای خیلی خوبی برای بازاریابی محصول آهناسفنجی دانست، بهطوریکه در کشورهای عربی تنها کشوری که میتواند از نظر ماده خام در مقیاس منطقهای با ایران رقابت کند، عمان است که در شروع اکتشافات قرار دارد، ایرانیها هم در این کشور در حال همکاری هستند، از سویی عمان در آینده نزدیک، رقیبی برای تامین مواد خام و محصولاتی همچون گندله آهناسفنجی و هر محصول دیگر بهویژه در بازار کشورهای عربی خواهد بود. بهتر این است که سرمایهگذاران ایرانی مخصوصا متخصصان بخش معدن و صنایعمعدنی کشور، قبل از اینکه بازار عمان و بخش معدن در اختیار کشورهای دیگر قرار گیرد، در آنجا سرمایهگذاری کنند تا بتوانند مدیریت بازار آینده منطقه را در دست بگیرند.
آهن اسفنجی؛ راهی به فولاد سبز
چندی پیش محمد مکملی، کارشناس حوزه معدن در ارتباط با مزیت نسبی ایران در تولید آهناسفنجی اظهار کرد: آهناسفنجی بهعنوان یک محصول میانی کلیدی در زنجیره تولید فولاد، نقشی محوری در کاهش ردپای کربن این صنعت ایفا میکند. آهناسفنجی، محصولی متخلخل و پرعیار از آهن است که از طریق احیای مستقیم سنگآهن با استفاده از گازهای احیاکننده مانند گاز طبیعی یا هیدروژن تولید میشود. این روش، خلاف کورههای بلند سنتی که وابسته به کک زغالسنگ هستند، امکان تولید آهن با خلوص بالا و آلایندگی کمتر را فراهم میکند.
مکملی ادامه داد: کاهش چشمگیر انتشار CO۲ یکی از مهمترین مزایای تولید آهناسفنجی است، علاوه بر این استفاده از هیدروژن بهعنوان گاز احیاکننده، قابلیت کاهش انتشار کربن تا صفر را نیز دارد. انعطافپذیری در مقیاس تولید و سازگاری با منابع گازی مختلف، از دیگر نقاط قوت آهناسفنجی محسوب میشود. این ویژگیها، امکان استقرار واحدهای تولیدی در مجاورت منابع سنگآهن و گاز را فراهم کرده و هزینههای حملونقل را نیز کاهش میدهد. برای تولید آهناسفنجی، دسترسی به منابع غنی سنگآهن و گاز طبیعی یا هیدروژن ضروری است. سرمایهگذاری در احداث کارخانههای احیای مستقیم، خطوط انتقال گاز و بندرگاههای صادراتی، از دیگر الزامات توسعه این صنعت بهشمار میرود، همچنین تکنولوژیهای نوین تولید هیدروژن سبز، نقشی کلیدی در آینده آهناسفنجی بازی خواهند کرد.
مزیت نسبی کشور ما نسبت به سایر کشورها
وی گفت: مزیت نسبی کشور ما نسبت به سایر کشورهای فعال در حوزه تولید آهن، انرژی ارزان است. در سالهای گذشته، نرخ هر تن کک، حدود ۴۰۰ دلار بود. برای مثال، ذوبآهن اصفهان برای تولید هر تن فولاد، حدود ۵۰۰ کیلو کک مصرف میکند که در مقایسه با نرخ گاز طبیعی، بسیار بالا است و در نتیجه، سودآوری کمتری دارد. علاوه بر بحث قیمت، مسئله مخرب بودن کورهبلندها برای محیطزیست نیز، مطرح است. در روش تولید احیای مستقیم، حدود هزار و۳۰۰ کیلو گاز گلخانهای CO۲ به ازای هر تن فولاد تولید میشود، در حالی که این رقم در کورهبلندها تا ۲هزار و۳۰۰ کیلو CO۲ بهازای یک تن فولاد میرسد، بنابراین میتوان گفت؛ گاز گلخانهای ناشی از روش احیای مستقیم بسیار کمتر از کورهبلند است.
وی افزود: ایران سالانه ۳۰ میلیون تن فولاد تولید میکند که از این مقدار، حدود ۱۵میلیون تن مصرف داخلی است و مابقی مازاد بر مصرف محسوب میشود. بخشی از این مازاد به کشورهای تحتنظارت اتحادیه اروپا صادر خواهد شد و در نتیجه، تولید محصولات دوستدار محیطزیست اهمیت ویژهای پیدا میکند. با تشدید چالشهای زیستمحیطی و تصویب مقرراتی همچون مالیات کربن در اتحادیه اروپا، تقاضا برای محصولات فولادی سازگار با محیطزیست هر روز در حال افزایش است. بر این اساس، دستیابی به تکنولوژی تولید آهناسفنجی با خوراک هیدروژن سبز، کلید طلایی موفقیت در آینده صنعت فولاد محسوب میشود. کشورهایی که هماکنون این مسیر را در پیش گرفتهاند، بیتردید از مزیتهای رقابتی فراوانی در بازارهای جهانی بهرهمند خواهند شد. شرکتهای بزرگ فولادسازی جهان نیز از قافله تحول سبز عقب نماندهاند. غولهای صنعتی همچون «آرسلورمیتال» و «تیسنکروپ» با سرمایهگذاریهای کلان در حوزه تحقیق و توسعه، بهدنبال بهینهسازی فرآیندهای تولید آهناسفنجی و کاهش ردپای کربن خود هستند. این شرکتها با درک صحیح از آینده بازار و الزامات سختگیرانه زیستمحیطی، خود را برای عصر فولاد سبز آماده میکنند.
سخن پایانی
شکل ظاهری آهناسفنجی موردمصرف کارخانهها بهصورت قطعات کروی و مانند اسفنج است و بههمیندلیل به آهناسفنجی معروف شده است. چنین موادی که حدود ۵درصد از فولاد جهان از آن تولید میشود، دارای عیار بالای آهن بوده و یکی از پراستفادهترین محصولات در صنایع فولادسازی است.