۳ گام تاافزایش کیفیت
سیامک حاج سیدجوادی-کارشناس و فعال حوزه صادرات سنگ تزئینی
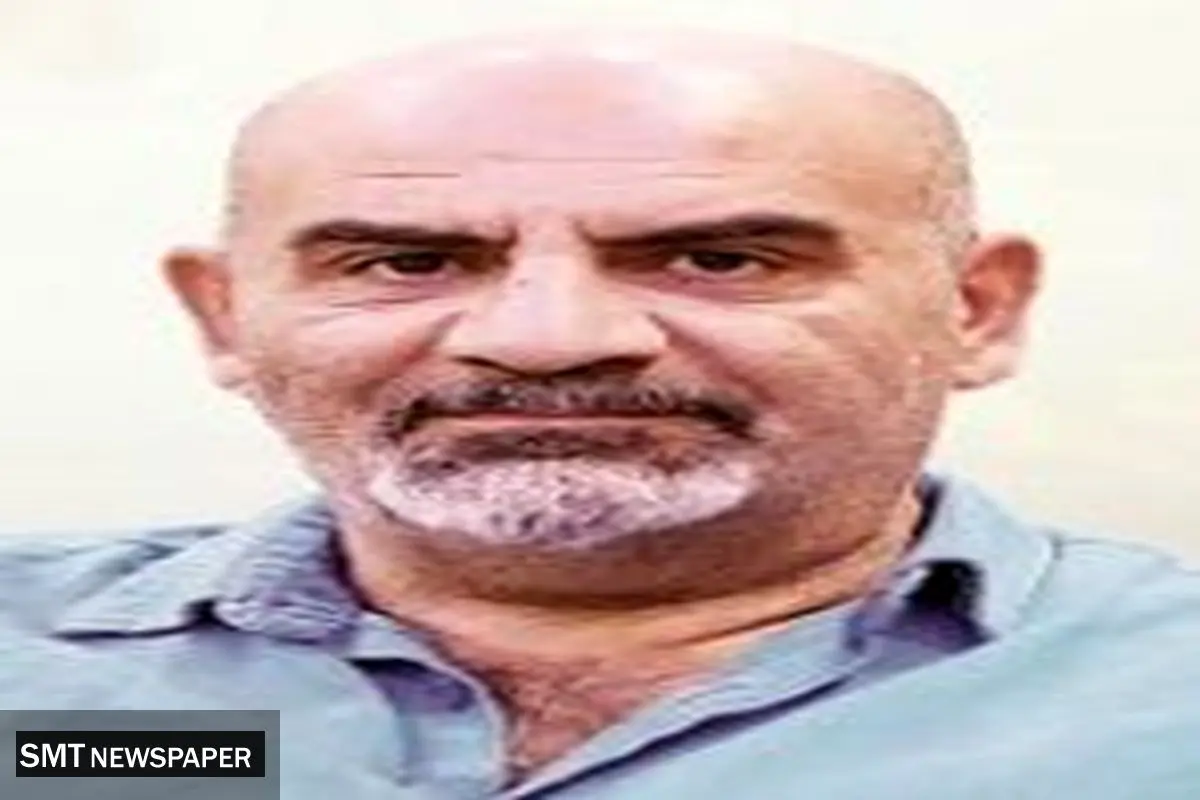
صادرات صنعت سنگ در ۲ فاز انجام میشود؛ یکی صادرات بلوک سنگ و دیگری، صادرات سنگ فرآوریشده. در فاز نخست، درصد کوپدهی معادن ما براساس استانداردهای بینالمللی بسیار پایین است. بهعبارتدیگر، اگر در یک معدن ۲هزار بلوک تولید میشود، بهدلیل استفاده از تکنیکهای غلط، شاید بتوان ۵۰۰ تن از آن را صادر کرد. بهعبارتدیگر، ۵ درصد تولید بلوک در معادن کشور، قابلیت ارائه در بازار جهانی را دارد. بنابراین، اگر در سال گذشته ۸ میلیون تن تولید داشتیم، تنها ۲ میلیون تن آن، قابلیت صادرات داشته و مابقی به مصرف بازار داخلی رسیده است. پس اگر بخواهیم با همین تکنولوژی موجود، صادرات سنگ خود را افزایش دهیم، باید ظرفیت تولید معادنمان را بالا ببریم، در غیر این صورت بهناچار باید روشهای استخراج جدیدی به کار ببریم که برمبنای آن، تکنولوژی استخراج، تغییر پیدا کند و درصد کوپدهی سنگ بالاتر برود. در کل دنیا ۳۵۰ میلیون تن سنگ درجا از معدن استخراج میشود که حدود ۱۵۴میلیون تن آن بهصورت کوپ درمیآید. یعنی نسبت کوپدهی معادن ۵۰ درصد است و نیمی از آن کوپی که از کوه استخراج میشود، به بلوک تبدیل میشود. این رقم در ایران بهصورت میانگین یک به ۴ یا ۵ است. پس اگر یکی از معادن کشور بخواهد در ماه، ۲ هزار تن سنگ بهصورت بلوک تولید کند، باید حدود ۱۰ هزار تن سنگ از کوه پایین بریزد و به این ترتیب، روشن است که ما از استانداردهای بینالمللی فاصله زیادی داریم. درباره سنگ فرآوریشده، صادرات به ۲ صورت انجام میشود؛ یکی بهشکل اسلب و دیگری، بهشکل تایل.خوشبختانه در تولید اسلب صادراتی فرآوریشده، اگر کوپ خوب و باکیفیت داشته باشیم، مشکلی در زمینه فرآوری باکیفیت استاندارد بازار نداریم. اما نکته اینجاست که تعداد واحدهایی که در زمینه تولید اسلب فعال هستند، در مقایسه با تعداد واحدهای فرآوری بسیار کم هستند. آخرین آمارهای وزارت صمت میگوید که ما چیزی حدود ۶ هزار واحد فرآوری داریم که از این تعداد، حدود ۶۰۰ واحد مجهز به اره هستند و میتوانند اسلب تولید کنند.
اگر فرض کنیم، این تعداد امروز به هزار واحد رسیده باشد، نزدیک ۱۵درصد واحدهای فرآوری ما، توانایی تولید اسلب با کیفیت بالا دارد و مابقی (حدود ۳۵ هزار واحد کارخانه) واحدهایی هستند که تایل تولید میکنند. نقطه ضعف اصلی سنگ فرآوریشده همینجا است. در واقع، باید اعتراف کرد که محصول تولیدی این کارخانههای فرآوری در زمینه کیفیت پولیش، صیقل سنگ، تولرانس ضخامت سنگ و تولرانس ابعاد دقیق سنگ مشکلات عدیدهای دارند.
درباره تلورانس ضخامت باید گفت که این عدد در ایران حدود مثبت-منفی ۱.۵میلیمتر است. یعنی اگر ضخامت ۲۰میلیمتر مدنظر باشد، باید تلورانسی از ۱۸.۵ تا ۲۱.۵ را در نظر بگیریم. استاندارد جهانی بههیچوجه این اندازه از تلورانس ضخامت (چیزی حدود ۳ میلیمتر) را نمیپذیرد. براساس استاندارد بینالمللی، این اختلاف نباید بیش از مثبت-منفی ۰.۵میلیمتر باشد؛ مثل این است که شما بخواهید با کولیس اندازه بگیرید، اما با تبر ببرید.مشکل از آنجا ناشی میشود که در کارخانجات ما، دستگاه کالیبر در عمل مورداستفاده قرار نمیگیرد، زیرا این تلورانس برای بازار مصرف داخلی که مشتری ۸۰ درصد سنگ تولیدی کشور است، اهمیت چندانی ندارد و با همین میزان اختلاف، سنگ تولیدی را مصرف میکند؛ به این ترتیب، انگیزهای برای کارخانهدار ایجاد نمیشود که کیفیت تولید خود را ارتقا دهد. استدلال کارخانهدار این است که بنا یا معماری که سنگ آنها را خریداری میکند، مشکلی با این میزان تلورانس ندارد، بنابراین نیازی نیست که روش تولید خود را تغییر دهد. در صورتی که، حداکثر هزینه خرید دستگاه کالیبر کردن سنگ، (اگر روی تولید سرشکن شود) یک دلار در مترمکعب هم نخواهد شد. علاوه بر این، تولیدکنندگان داخلی هم میتوانند این دستگاه را بسازند. حال چرا اقدامی برای نصب این دستگاه انجام نمیشود؟ دقیقا به همان دلیلی که در بالا ذکر شد. تولیدکننده بهعلت بیتوجهی بازار داخلی به موضوع ضخامت استاندارد، تلاشی برای بهبود تولیدات خود در این زمینه نمیکند، اما اگر بخواهد وارد بازار بینالمللی شود، اوضاع به این راحتی نخواهد بود و باید استاندارد جهانی ضخامت سنگ را رعایت کند.موضوع بعدی تلورانس ابعاد است. تولیدات ما در زمینه تلورانس طول و عرض سنگ هم دچار همان نقصی است که در تلورانس ضخامت دارد. در اینباره هم، تولیدات سنگ داخلی حدود ۲ میلیمتر اضافه تلورانس دارد و بازار بینالمللی این میزان اختلاف را قبول ندارد. حداکثر تغییرات ابعادی که موردقبول خریدار بینالمللی است، مثبت-منفی ۵. ۰یا در مجموع یک میلیمتر است. برای جبران این نقص، به ۲ دستگاه طولیبر و عرضیبر نیاز است، اما این دو دستگاه را هم میتوان در داخل کشور ساخت. موضوعی که در این زمینه باید به آن توجه داشت، استاندارد بندکشی است. وقتی قرار باشد، استانداردهای بینالمللی رعایت شود، حداکثر ضخامت بندکشی بین یک تا ۲ میلیمتر است. بنابراین، وقتی سنگی با ۵. ۰ میلیمتر تلورانس نصب شود، بین یک تا ۱.۵ میلیمتر فضا برای بندکشی باقی میماند، اما بندکشیها در ایران حدود ۴ تا ۵ میلیمتر است؛ پس در اینجا هم بازار داخلی نیازی به دقت اندازهگیری ندارد.بنابراین، اگر تولیدکنندهای بخواهد تا به کیفیت استاندارد سنگ فرآوریشده (تایل) دست پیدا کند، باید ۳ دستگاه به خط تولید خود اضافه کند که عبارتند از: دستگاه کالیبر، طولیبر و عرضیبر. جمع هزینه این دستگاهها چیزی بالغ بر ۴ تا ۵ میلیارد تومان است؛ یعنی هر واحد تولیدی باید چنین مبلغی را سرمایهگذاری کند تا به استاندارد مطلوب در بازار جهانی برسد.