مواد اولیه پلاستیک و مصرف آن در صنایع رنگسازی
مستربچ به محصولی گفته میشود در آن پیگمنت و رزین پایه به همراه افزودنیهای دیگر ادغام میشوند.
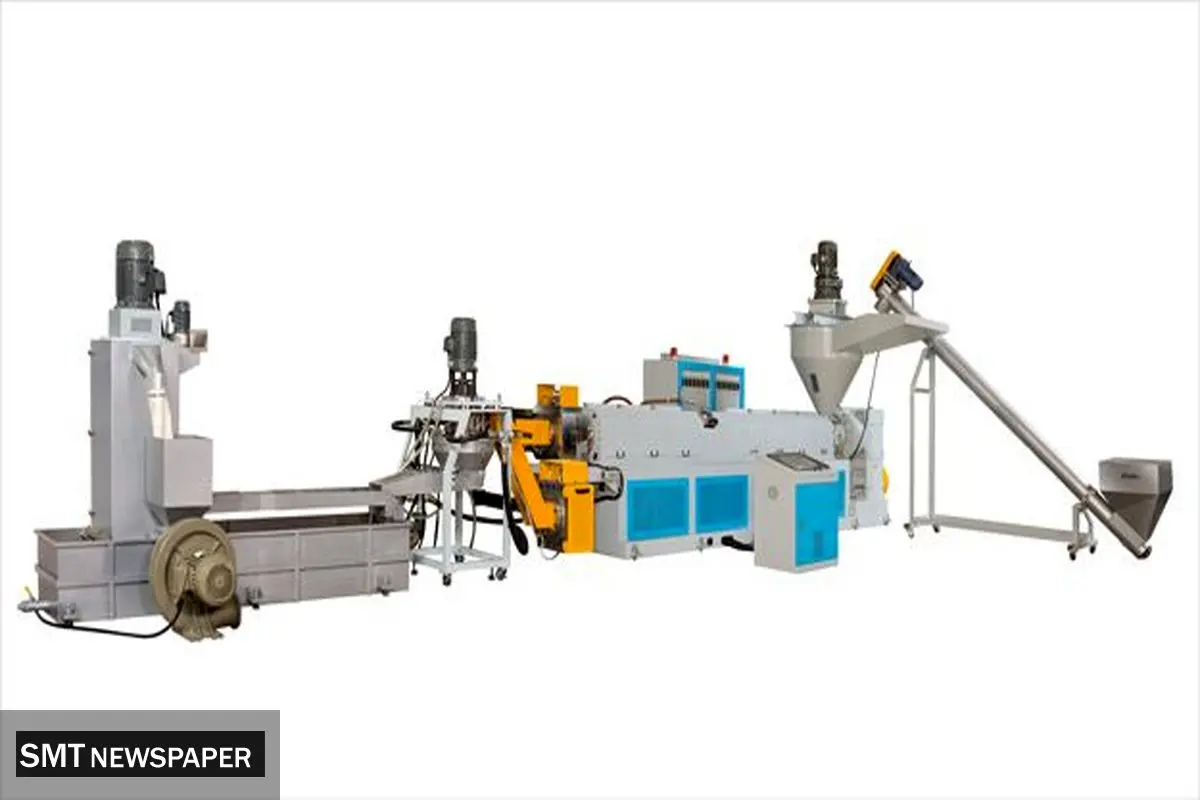
بهطورکلی مراحل تولید این ماده شامل موارد زیر هستند:
فرمولاسیون
اولین مرحله تولید، فرمولاسیون است، فرمولبندی به معنای تعیین فرمول دقیقی برای ترکیبات مورد نیاز است، در این مرحله توزین دقیق تمام اجزاء مشخص میشوند.
خوراکدهی
در این مرحله باید میزان تغذیه با خروجی دستگاه مشخص شود. در این مرحله خوراک اصلی دستگاه که شامل پیگمنت و رزین پایه هستند اضافه میشوند.
اختلاط
برای اختلاط، مواد اولیه داخل اکسترودر ریخته میشوند و پس طی مراحل زیر از بخش اکستروژن به شکل گرانول خارج میشوند.
1- خیس کردن رنگدانهها و پیلمر پایه (مواد پلیاتلین 209)
2- مخلوط کردن پیلمر پایه با افزودنیها (مواد پلیاتلین 0035)
3- ذوب کردن
4- مخلوط کردن برای جلوگیری از کلوخه شدن
تکنیکهای اختلاط مواد اولیه (مواد پلیاتلین F7000)
برای انجام این کار دو روش کلی وجود دارد.
-
روش پیش اختلاط
در این روش مواد فرمولاسیون تولید مستربچ با استفاده از مخلوطکن با سرعت بالا باهم مخلوط میشوند. این کار به دو روش سرد و گرم صورت میپذیرد.
روش تسهیم خوراک
در این روش ابتدا پلیمر پایه به صورت جداگانه وارد مخزن میشود و پس از وزنکشی، به اندازهای که در فرمولاسیون تعیین شده است ذوب میشود، سپس وارد دستگاه اکسترودر شده و ذوب میشود.
الک کردن
برای این که اندازه مستربچهای تولیدشده یکسان باشد و دانههای ریزتر یا درشتتر از حد معمول در آنها وجود نداشته باشد، در مرحله آخر تولید به الک کردن دانهها میپرازند.
اختلاط مؤثر به کمک ترکیبات سازگارکننده
سازگارکنندهها با عنوان علمی ترکیبات آمفیفیلیک، دارای یک سر آب دوست و یک سر آلی دوست هستند و به دلیل ماهیت شیمیایی خاصشان، باعث:
- افزایش پایداری حرارتی
- سازگارسازی پلیاولفینها و پلیمرهای مهندسی
- تشکیل لایه پایدار بر روی سطح افزودنی، پیگمنت یا پرکننده از طریق کنش متقابل با آنها و ایجاد اتصال آنها به ماتریس پلیمری میشوند.
روش پیش اختلاط
در این روش برای تولید مستربچ از یک مخلوطکن داخلی با سرعت بالا استفاده میشود. از طریق این مخلوطکن، یک مخلوط همگن از فرمولاسیون مستربچ که شامل پودر پلیمر، پیگمنت و عامل پراکنش میباشد، تولید میشود.
در حالت سرد فقط مخلوطی همگن از اجزا تشکیل میشود. اما در نوع گرم این روش به دلیل ایجاد انرژی و اصطکاک کافی عامل پراکنش ذوب میشود و خیسشدگی پیگمنتها شروع میشود. بعد از آن این مخلوط همگن به اکسترودر فرستاده میشود تا وزنکشی شود.
بعد از این مرحله مخلوط همگن به قسمت تغذیه اکسترودر و ماردون شده میرود و ذوب میشود. در این حالت بر هم کنش و پراکنش پیگمنتها داخل مذاب پلیمری (مواد پلیاتلین X3) انجام میشود.
در آخر مذاب خارج شده از دای خرد میشود و در حمام آب سرد میشود. سپس همگنسازی انجام میشود و به شکل گرانول بستهبندی میشود.
روش تسهیم خوراک
در روش تسهیم خوراک جهت تولید مستربچ در ابتدا پودر پلیمر بهصورت جداگانه به مخزن تغذیه وارد میشود و وزنکشی میشود. بعد از آن وارد ناحیه تغذیه اکسترودر دو مارپیچه شده و عملیات ذوب آن آغاز میشود. سپس وزنکشی شده و به وسیله خط جانبی تغذیه اکسترودر، به مذاب پلیمری درون اکسترودر اضافه میشوند .
- در روش قبلی (پیش اختلاط) به دلیل مقاومت حرارتی پایینتر پیگمنتها، ممکن بود پیگمنتها دیگر قابلیت و قدرت رنگدهی لازم را نداشته باشند و یا کیفیت رنگ آنها کاهش یابد. اما در روش تسهیم خوراک این مشکل برطرف شده است.
- یکی از مزایای روش تسهیم خوراک این است که پیگمنت دیگر به ناحیه ذوب وارد نمیشود و نیازی نیست از آن عبور کند. این امر خطر کلوخه شدن آن را کاهش میدهد.
- ماردون اکسترودر دو ماردون در این فرآیند نسبت طول به قطر ۴۰ الی ۴۸ را داراست که جهت تولید مستربچهای کربن بلک و تیتانیوم دیاکسید مورد استفاده قرار میگیرد.
- در روش تسهیم خوراک اغلب مستربچ با کیفیت عالی و بسیار بالاتر از روش پیش اختلاط تولید میشود.
- روش تسهیم خوراک به علت پیچیده بودن سیستم، هزینه سرمایهگذاری اولیه بیشتری دارد.
- در این روش تولید محصولات به مقدار ۵۰۰ الی ۵۰۰۰ کیلوگرم بر ساعت صورت میگیرد.
پایۀ پلیمری مصرفی، غالباً از جنس مواد زیر هستند:
- انواع پلیاتیلن، پلیاتیلن 2102، پلیاتیلن 020 ، پلیاتیلن 1922 ، پلیاتیلن 190
- پلیپروپیلن، پلیپروپیلن Z30S، پلیپروپیلن C30S، پلیپروپیلن 440L
- پلیاستایرن - کریستال 1540- هایمپک 7240
- اتیلن وینیل استات
- واكسهایی با وزن مولكولی پایین
- پلیمر آلكیدی
- پلیمرهای مخصوص دیگر…
۲-افزودنی
به منظور تغییر خواص پلیمرها، مواد شیمیایی افزودنی به مستربچها اضافه میشوند که عبارتند از افزودنیهای بهبوددهنده خواص، پیگمنتها و پرکنندهها.
۳-عامل سازگارکننده
سازگارکنندهها با عنوان علمی ترکیبات آمفیفیلیک، دارای یک سر آب، دوست و یک سر آلی، دوست هستند و به دلیل ماهیت شیمیایی خاصشان، باعث:
- افزایش پایداری حرارتی
- سازگارسازی پلیاولفینها و پلیمرهای مهندسی
- تشکیل لایه پایدار بر روی سطح افزودنی، پیگمنت یا پرکننده از طریق کنش متقابل با آنها و ایجاد اتصال آنها به ماتریس پلیمری میشوند.
مزایای سازگارکنندهها در فرآیند تولید مستربچ
با افزودن سازگارکنندهها به مستربچ، فرآیندپذیری آنها از طریق بهبود ترشوندگی، یکنواختی و تثبیت، تسهیل میشود که هریک شامل موارد زیر میشوند:
- ترشوندگی سریع
- امکان افزایش سرعت فرآورش
- امکان افزایش بارگیری
- بهبود یکنواختی
- کلوخهها و تجمع ذرات کمتر
- افزایش استحکام رنگ
- تثبیت عالی
- پیشگیری از کلوخهسازی مجدد
- رقیقسازی آسان و بهبود سازگاری در کاربرد نهایی
- تطابق رنگ دقیق
انواع مستربچ
انواع مستربچها عبارتند از:
- مستربچ افزودنی
- مستربچ رنگی
- مستربچ پرکننده
انواع مستربچ افزودنی
- شفافکننده PP یا هستهزا
- نانو افزودنی
- لیزکننده
- آنتیبلاک
- روشنکننده نوری یا براقکننده
- آنتیاستاتیک
- پایدارکنندۀ نور
- آنتیاکسیدانت
- کمک فرآیند پلیمر
- ضد سایش
2- مستربچ رنگی
رایجترین روش تولید قطعات رنگی از مواد پلاستیکی، افزودن مستربچهای رنگی است.
- با به کار بردن مستربچها میتوان در وقت، انرژی و هزینۀ لازم برای مخلوطكردن این پودرها و نیروی كار صرفهجویی كرد و استفاده از این تركیبات اقتصادی است.
- بهدلیل عدم پخششوندگی مناسب برخی از افزودنیها، امکان اضافهکردن مستقیم آن به محصول وجود ندارد که این مشکل با استفاده از مستربچ حل میشود.
- سهولت ذخیرهسازی، جابجایی و کاربری به دلیل شکل گرانولی آن
- سادهترشدن خوراکدهی و حل مشکل تغییر غلظت افزودنی و یکنواختی رنگ یا خواص در حین تولید
- عدم پخش پیگمنتها در هوا و در نتیجه ایجاد خطر سلامتی و ایمنی کارکنان و آلودهسازی خطوط تولید مجاور
- پخش و یکنواختی بهتر رنگ، افزودنی یا پرکننده در سراسر محصول نهایی
- مصرف مقدار کمتر پیگمنت یا افزودنی
- بهبود فرآیند ذوب به دلیل سازگاری عامل اتصال دهنده مستربچ با پلیمر
- ثبات بیشتر خواص یا رنگ
- کنترلپذیری بهتر کدری و شفافیت محصولات رنگی
- کاهش دفعات خوراکدهی در فرآیند با استفاده از مستربچ حاوی افزودنیهای تغلیظشده پایدارUV، آنتیاکسیدانت، به تأخیر اندازنده شعله یا شفافکننده نوری
- افزایش تکرارپذیری فرآیند از طریق از پیش تعیینکردن نسبت اجزای افزودنی مستربچ
- حذف هزینه پاکسازی و تمیزکاری
ویژگیهای مستربچ خوب
فاکتورهای مؤثر در انتخاب مستربچ با کیفیت مناسب عبارتند از:
- مطابقت پایه پلیمری مستربچ با مواد و کالای تولیدی
- ثبات رنگ یا خواص در دفعات مصرف
- مشخصات فنى مطلوب که این مشخصات فنی عبارتند از مقاومت انتقال سطح، درصد رطوبت، دمای ذوب، پراکندگی در ماتریس پلیمری، شکل ظاهری و درخشندگی (جلا)، مقاومت حرارتی سطح
- غلظت یکنواخت و درصد مناسب افزودنی یا پیگمنت
- ميزان مصرف كم
- منحصر بهفرد بودن رنگ و شيد
- عدم ایجاد مشکلات در فرآیند تولید محصول نهایی