ضعف تقاضا در بازار آهناسفنجی ایران
عرضههای انجام شده آهن اسفنجی در ایران در قیمتهای پایینتر، موجب شد تا قیمت میانگین موزون معاملات آهن اسفنجی پایینتر از سقف قیمت پایه قرار گیرد. این موضوع نشاندهنده وجود رقابت شدید در بازار و تلاش شرکتها برای جذب مشتریان بیشتر است.
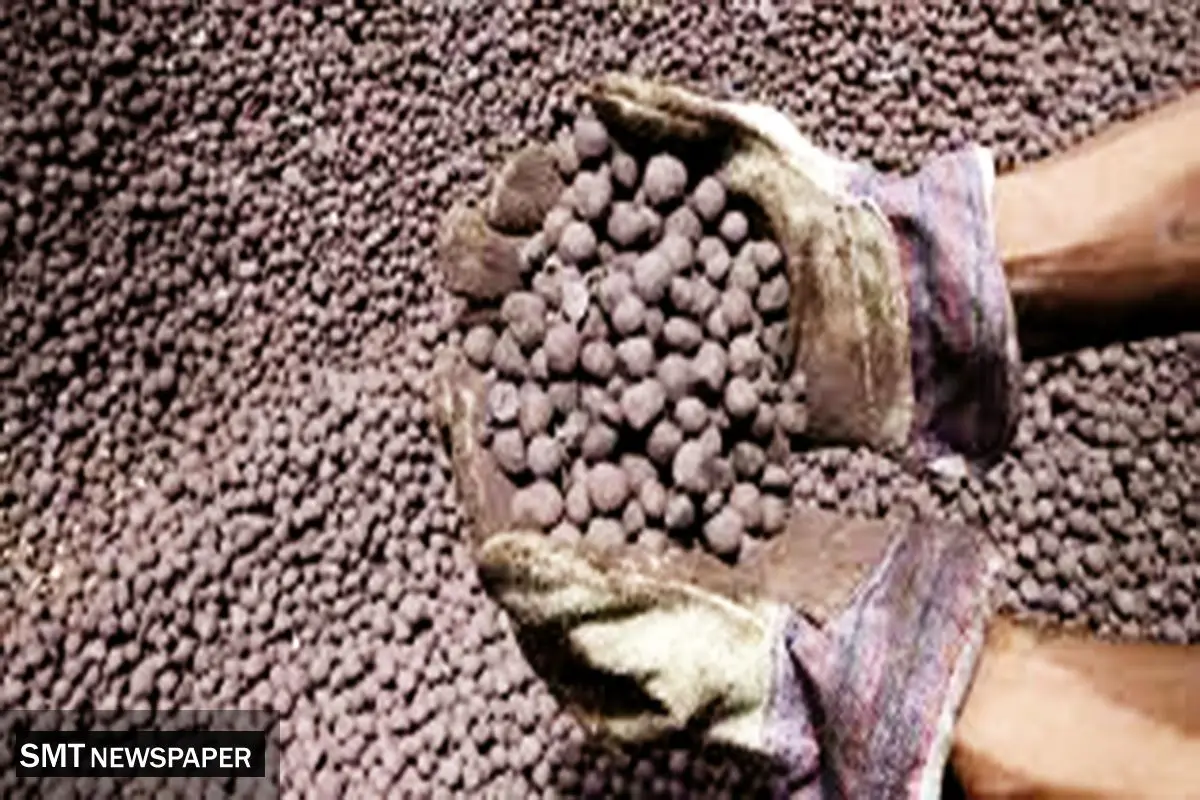
در چند وقت اخیر، بازار آهن اسفنجی در بورس کالا شاهد کاهش قیمت میانگین به میزان ۱۹۶ تومان به ازای هر کیلو، معادل ۱.۱ درصد بود. این کاهش قیمت، آهن اسفنجی را به ۱۷۴۷۴ تومان به ازای هر کیلو بدون احتساب مالیات بر ارزش افزوده رساند.
تغییرات قیمتی آهن اسفنجی
این تغییرات قیمتی در حالی رخ میدهد که حجم معاملات آهن اسفنجی در این هفته به حدود ۱۳۵ هزار تن رسید که معادل ۷۰.۸ درصد از حجم عرضهها بود.
سقف قیمت پایه عرضه آهن اسفنجی در این هفته ۱۷۷۱۳ تومان به ازای هر تن تعیین شده بود و بسیاری از شرکتها عرضههای خود را در این قیمت انجام دادند.
قیمت آهن اسفنجی پایینتر از سقف ایستاد
با این حال، عرضههای انجام شده در قیمتهای پایینتر، موجب شد تا قیمت میانگین موزون معاملات آهن اسفنجی پایینتر از سقف قیمت پایه قرار گیرد. این موضوع نشاندهنده وجود رقابت شدید در بازار و تلاش شرکتها برای جذب مشتریان بیشتر است.
علاوه بر این، حدود ۴۷ هزار تن از معاملات آهن اسفنجی در این هفته در قالب مچینگ انجام شد. این آمار، به همراه ۵۵ هزار تن معامله نشده، نشاندهنده ضعف زودهنگام تقاضا در بازار آهن اسفنجی است.
به نظر میرسد که عوامل مختلفی از جمله نوسانات اقتصادی و تغییرات در تقاضای صنایع مختلف، بر این روند تأثیرگذار بودهاند.
تغییر در الگوهای مصرف مواد اولیه فولادی
نکته قابل توجه دیگر، نسبت قیمت آهن اسفنجی به شمش فولادی است که در هفته جاری به ۵۹.۹ درصد رسید. این نسبت در اسفندماه سال گذشته ۶۵ درصد بود و نشاندهنده تغییرات قابل توجه در بازار فولاد و آهن است. این کاهش نسبت میتواند به معنای افزایش رقابت در بازار و تغییر در الگوهای مصرف باشد.
به طور کلی، بازار آهن اسفنجی در هفته جاری با چالشهایی مواجه بوده و نیاز به تحلیل دقیقتری از عوامل مؤثر بر تقاضا و عرضه دارد.
با توجه به روندهای اخیر، به نظر میرسد که فعالان بازار باید به دقت تحولات را زیر نظر داشته باشند تا بتوانند تصمیمات بهتری در زمینه خرید و فروش اتخاذ کنند.
آهن اسفنجی چیست؟
آهن اسفنجی یا گندله متخلخل به مادهای گفته میشود که از احیای سنگ آهن به روش مستقیم (Direct Reduced Iron) یعنی بدون نیاز به عملیات ذوب کردن به وجود میآید. در طی فرآیند احیای مستقیم و به دلیل خروج گاز اکسیژن، سنگ آهن به قطعات کروی شکل، با شکل ظاهری متخلخل مانند اسفنج که بر روی سطح خود دارای سوراخهای کوچکی است تبدیل میشود. همین شکل و ویژگی ظاهری نیز دلیل نام گذاری این محصول شده است.
فرمول شیمیایی آهن اسفنجی در واقع همان فرمول شیمایی آهن (Fe) است؛ زیرا این محصول از طریق احیای مستقیم آهن به وجود میآید و در نهایت ممکن است مقداری ناخالصی نیز داشته باشد.
آهن اسفنجی پس از ذوب شدن و در طی فرآیند ریخته گری به سه محصول شمش، تختال (اسلب) و میلگرد تبدیل می شود که این سه محصول برای استفاده در مصارف مختلف به کارخانجات ارسال شده و در آنجا به محصولات پرکاربردتر دیگری تبدیل می شوند. گندله که دارای عیار بسیار بالایی از آهن است، امروزه با توجه به کمبود ضایعات آهن و مسائل زیست محیطی بسیار مورد توجه قرار گرفته است و به عنوان جایگزین مناسبی برای ضایعات آهن شناخته میشود.
روش تولید آهن اسفنجی
به طور کلی سنگ آهن به دو روش گاز طبیعی و زغال سنگ احیا شده و منجر به تولید آهن اسفنجی میشود. فرایند احیای سنگ آهن به وسیله گاز طبیعی به سه روش میدرکس،HYL و Purofer انجام می شود که در میان این روشها، روش میدرکس نسبت به سایر روشها کاربردی تر است. در فرایند احیا به وسیله زغال سنگ نیز از روشهای Jindal ،DRC و SL/ RN جهت تولید این محصول استفاده میشود. در ادامه به بررسی این روشها میپردازیم و درباره هرکدام توضیحاتی ارائه خواهیم داد.
۱) تولید آهن اسفنجی به روش میدرکس
در این روش که یکی از مناسبترین روشها برای احیای سنگآهن به شمار میآید، در ابتدا گاز متان وارد واحد شکست شده تا به دو گاز احیا کننده اکسیژن و هیدروژن تجزیه شود. پس از آن متان تجزیه شده در یک کوره استوانه ای دمیده می شود. همزمان با دمیدن متان تجزیه شده، سنگ آهن از بالا داخل کوره انداخته میشود تا با گاز متان تجزیه شده برخورد کند.
گاز طبیعی متان تجزیه شده هنگامی که در کوره دمیده شد، داغ میشود و سنگهای آهن به هنگام برخورد با آن اکسیژن خود را از دست می دهند. در آخر گلولههایی متخلخل از آهن خالص که پخته و سخت شدهاند تحت عنوان محصول نهایی ارائه میشوند. آهن اسفنجی که با روش میدرکس تولید می شود به دلیل سختی بیشتر در هنگام انجام عملیات ذوب به انرژی بیشتری نیز نیاز خواهد داشت.
وش میدرکس یکی از پربازدهترین روشها برای تولید آهن اسفنجی به شمار میآید و حدود 80 درصد از آهن اسفنجی ایران نیز به همین روش تولید میشود.
۲) تولید آهن اسفنجی به روش HYL
در روش HYL نیز مانند روش میدرکس، از گاز طبیعی برای احیای سنگ آهن استفاده می شود، با این تفاوت که تجهیزات مورد نیاز در این فرایند و مراحل تولید محصول نهایی دارای پیچیدگی و هزینه بیشتری نسبت به روش میدرکس میباشند.
پروسه احیای سنگ آهن شامل دو بخش کلی یعنی یک بخش آماده سازی و تجزیه گاز طبیعی و بخش کوره احیای آهن می باشد. در واحد آماده سازی گاز طبیعی، گاز طبیعی متان با بخار آب ترکیب شده و منجر به تجزیه عناصر تشکیل دهنده میشود. سپس این عناصر در کوره با سنگ آهن دمیده خواهد شد که محصول نهایی و به دست آمده آهن اسفنجی است.
آهنی که در این فرایند تولید میشود دارای کربن بیشتری در محتوای خود است و به اصطلاح کربوره شده است.
۳) تولید آهن اسفنجی به روش SL/Rn
در این روش به جای گاز طبیعی از زغال سنگ برای فرایند احیای سنگ آهن استفاده میشود. این فرایند شامل یک بخش تغذیه است که در آن مواد اولیه با یکدیگر ترکیب میشوند. مواد اولیه شامل سنگ آهن یا کلوخه آهن است که ابتدا به بخش تغذیه کننده وارد شده و پس از آن آهک و دولومیت به همراه زغال سنگ به مواد اولیه اضافه می شود تا برای مرحله احیا به کوره افقی فرستاده شوند.
یکی از دلایل استفاده از دولومیت و آهک در ترکیب مواد اولیه کمک به حفظ درصد گوگرد مورد نیاز برای انجام فرآیند است. در بخش کوره افقی که دارای شیب خیلی کمی است و به صورت دورانی حرکت می کند، مواد اولیه در آنجا ریخته میشود و به صورت آهسته در کوره به حرکت در می آیند. در این مرحله دمای کوره تا حدی بالا میرود که زغال سنگ کک نشود و شروع به سوختن و تولید دی اکسید کربن کند. تولید دی اکسید کربن آنقدر ادامه پیدا می کند و دما بالا میرود تا سنگ آهن به صورت کامل احیا شود.
سخن پایانی
به طور کلی، آهن اسفنجی جایگزین مناسبی برای ضایعات آهن به شمار میآید. در نتیجه با استفاده از آن میتوان درصد بالایی از مواد اولیه جهت فراهم آوردن ذوب مورد نیاز واحدهای فولادسازی را به جای استفاده از ضایعات تهیه نمود. از مهمترین کاربردهای این محصول، استفاده شدن در کورههای القائی است که توانایی جایگزینی ۵۰ درصدی آن با قراضه وجود دارد.