چالشهای معدن و صنایعمعدنی
بررسیها نشان میدهد محدودیتهای فزاینده برق که تا مهرماه هم ادامه داشت، موجب افت ۵.۷درصدی تولید فولاد ایران در نیمه نخست سال شده است. کمبود برق یکی از موانع اساسی تولید فولاد کشور در تابستان سالجاری بود.کیوان جعفریطهرانی، کارشناس ارشد بازار بینالمللی فولاد و سنگآهن در بررسی چالشهای معدن و صنایع معدنی به مواردی اشاره کرده که در ادامه میخوانید
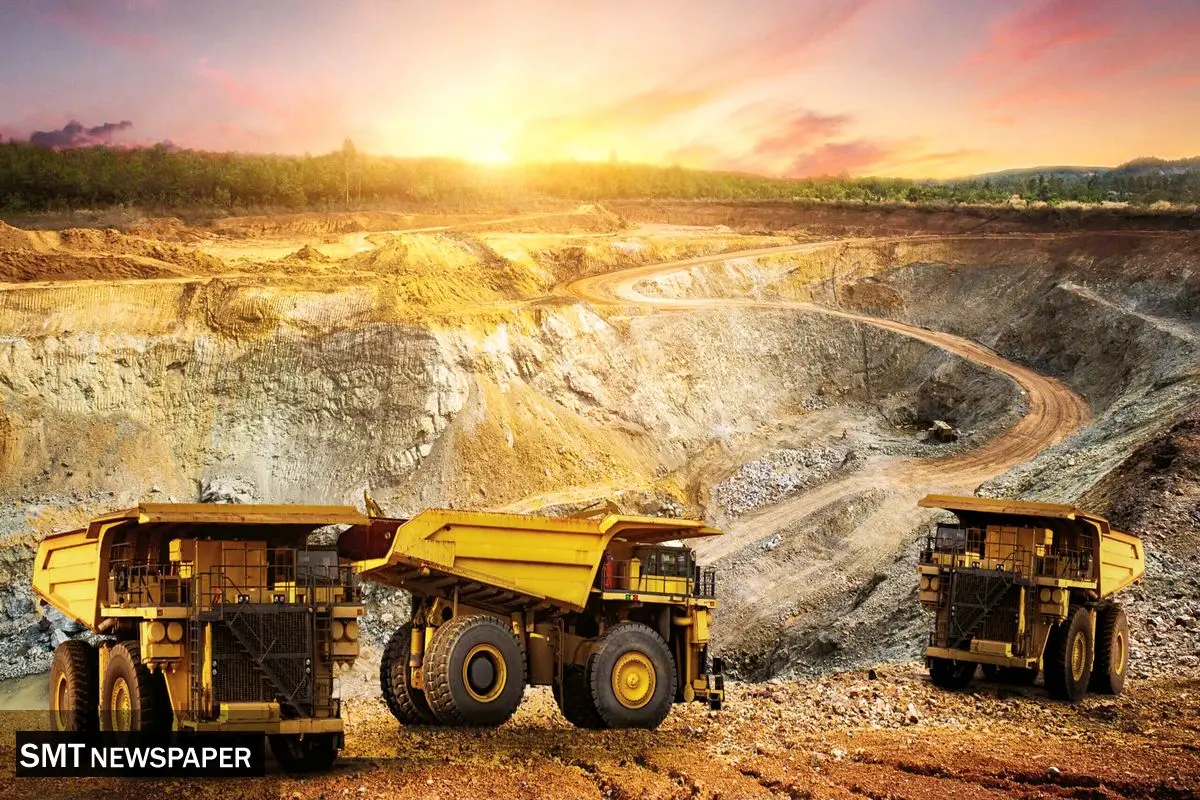
سهگانه «چالشهای تولید آهناسفنجی»، «وضعیت واردات ماشینآلات معدنی» و همچنین بحث «ارز نیمایی واردات»، از مهمترین مسائل این روزهای حوزه معادن و صنایع معدنی محسوب میشود که در ادامه به ترتیب به این سهگانه خواهم پرداخت. مهمترین چالش تولید آهناسفنجی، موضوع انرژی است. متاسفانه کمبود انرژی بهویژه کمبود گاز در زمستان باعث میشود خریداران خارجی بالقوهای که علاقهمند به خرید آهناسفنجی ایران بودند کاهش پیدا کنند، در واقع خریداران این بازار و بازار سنتی ایران از قدیم هندوستان، پاکستان و عمان بودند و این محمولهها مرتب صادر میشد، به این دلیل که فاصله جغرافیایی دورتر برای این کشورها بهعلت مسائل «حملونقل دریایی» توجیه اقتصادی ندارد و ریسک بالایی دارد. به هر حال آهناسفنجی در برابر اکسیژن هوا قابلیت اشتعال دارد و به همین منظور برای غیرفعالسازی آن از گاز نیتروژن استفاده میکنند و کشتیهایی که حامل آهناسفنجی هستند، به لولهکشی گاز نیتروژن باید تجهیز شوند که هزینه مضاعفی خواهد داشت. با این اوصاف این کمبود انرژی باعث میشود که خریداران سنتی محمولههای صادراتی ایران هم علاقه و انگیزه خرید نداشته باشند.
از سوی دیگر بحث کمبود انرژی جهت تامین بازار داخلی را هم شاهد هستیم که این معضل باعث وقفه در زنجیره تولید فولاد میشود. در واقع بحث کمبود انرژی یکی از مسائل عمدهای است که باید به آن پرداخته شود و بقیه کارشناسان هم درباره این مسئله بارها صحبت کردهاند. با توجه به اینکه قیمت آهن قراضه تعیینکننده قیمت آهناسفنجی ایران است ولی حال بازار آهن قراضه در حال حاضر خوب نیست و شرایط بهگونهای است که قیمتها از روند تولید حمایت نمیکند. در حوزه واردات ماشینآلات معدنی باید گفت موضوع وارد کردن ناوگان جدید و نو به صنایع معدنی در حال حاضر محلی از اعراب ندارد به دلیل اینکه با نرخهای فعلی ارز، واردات واقعا مقرون به صرفه نیست. برندهای معروف جهان و ترجیحا خیلی از برندهای چینی و کرهای که در حال حاضر محبوب شدهاند قیمت مناسبتری نسبت به برندهای ژاپنی و اروپایی دارند، هرچند محدودیتهای واردات ماشینآلات معدنی دست دوم تا حدی برای جامعه معدنی سخت شده است با این حال این مشکلات در حال رفع است، ولی مسئله فقط این نیست. مشکل تامین سوخت این ماشینآلات جدید هم خود یکی از مسائل مهم در این حوزه است. این ماشینآلات نیاز به سوخت با استاندارد یورو۵ به بالا دارند و ما برای تامین سوخت گازوئیل این خودروها (ماشینهای سنگین) با مشکل مواجه خواهیم شد.
برای مثال درباره خودروهای سواری جدید در واقع اصطلاحا از اکتان برای افزایش قابلیت احتراق بنزین خودرو استفاده میکنند، ولی برای ماشین سنگین این مسئله وجود ندارد و توجیه اقتصادی ندارد که بخواهند برای ماشینهای سنگین راهسازی و معدنی جدید از مکمل سوخت استفاده کنند. اینها مسائلی است که باید به آن توجه شود و اگر هم قرار است ماشینآلاتی وارد کشور شود، این ماشینآلات باید امکان و قابلیت استفاده از سوختهای داخل کشور را داشته باشند؛ تا مشکلات متعددی که بارها در زمینه تعمیر و نگهداری ماشینآلات با آن برخورد کردیم، کاهش پیدا کند. چالشهای ارز جهت فروش در سامانه نیما یکی از موضوعات مهم و در سهگانه چالشهای صنایع معدنی قرار دارد. در این باره یک بخشنامه مهم وجود داشت که بر آن مبنا قرار بود کل زنجیره فولاد و حتی فلزات پایه، ۱۰۰درصد ارز را در نیما بهفروش برسانند ولی بعد از آن قرار شد فلزات پایه بتوانند به صورت توافقی فروش داشته باشند ولی در مورد کل زنجیره فولاد باید نسبت به واردات ماشینآلات و تجهیزات موردنیاز خودشان اقدام کنند.
به نظر من اگر این روند متوقف نشود، بیش از گذشته در صادرات تاثیرات سوء میگذارد به دلیل اینکه صادرکننده باید آن انگیزه لازم را برای خرید یک محصول و صادرات و فروش ارز خود با نرخ توافقی داشته باشد. فراموش نکنیم که حجم قابلتوجهی از صادرات کشور توسط بخش خصوصی اتفاق میافتد و خیلی از شرکتهای بخش خصوصی صرفا شرکتهای تجاری هستند و در فعالیتهای معدنی و صنایع معدنی فعال نیستند و علاقه یا نیازی به واردات ماشینآلات و تجهیزات معدنی ندارند. اگر این اجبار واردات ماشینآلات و تجهیزات معدنی در رابطه با صادرکنندگان زنجیره فولاد اصلاح نشود تاثیر بسیار بدی در کاهش صادرات خواهد داشت چنانکه از ابتدای امسال تا پایان ماه هشتم شاهد این افت صادرات بودیم. مهمترین اصل این است که نباید فراموش کنیم که در شرایط مناسبی نیستیم مخصوصا با حضور ترامپ عرصه برای صادرات کشور روزبهروز تنگتر خواهد شد. محدودیتهای داخل کشور چه در رابطه با انرژی که در تولید محصولات زنجیره فولاد از جمله آهناسفنجی تاثیر میگذارد و چه کاهش انگیزه صادرات به علت تاکید بر واردات ماشینآلات و تجهیزات موردنیاز پروژهها، همه ضربه مضاعفی خواهد زد و یک نوع خودتحریمی است.
خسارت قطعی برق به صنعت فولاد
بدون شک بسیاری از شرکتهای فولادسازی بهدلیل قطع برق به اهداف خود در 6 ماه سال ۱۴۰۳ دست نیافتند. محدودیتهای ناشی از قطع شدن برق برای واحدهای فولادسازی، با پیامدهای منفی همراه شد. یکی از این پیامدها کاهش میزان تولید و محقق نشدن اهداف این شرکتها بوده است. نکته قابلتوجه آنکه با تعطیلی و کاهش تولید صنعت فولاد
به دلیل قطع برق، هزاران شغل غیرمستقیم که بهواسطه فعالیت فولادسازان شکل گرفته نیز به تعطیلی کشیده شده و واحدهای پاییندست با آسیب جدی و خطر تعطیلی همراهمی میشوند. در همین راستا بررسی وضعیت تولید محصولات زنجیره آهن و فولاد ایران در نیمه نخست امسال نشان میدهد محدودیتهای فزاینده برق که تا مهرماه هم ادامه داشت، سبب افت ۵.۷درصدی تولید فولاد ایران شده است. همچنین محدودیتهای برقرسانی، تولید ششماهه فولاد میانی کشور را حدود ۱.۱میلیون تن به ارزش بیش از ۴۵۰میلیون دلار کاهش داده است. بیشترین نرخ افت تولید زنجیره فولاد در میلگرد، نبشی، ناودانی و شمش فولادی بهترتیب با ۱۱.۷، ۹.۶ و ۸.۵درصد کاهش بوده است. افزایش ۱۰.۲درصدی تولید آهناسفنجی در برابر کاهش ۵.۷ درصدی تولید فولاد میانی خبر خوبی برای فولادسازانی است که هنوز زنجیره خود را تکمیل نکردهاند. کاهش ۴درصدی تولید گندله سنگآهن همزمان با رشد ۱۶درصدی صادرات آن موجب نگرانی تولیدکنندگان آهناسفنجی است! رشد ۵.۵درصدی تولید در ورق گرم خبر خوبی است که تداوم آن نیازمند کنترل هدفمند واردات است. همچنین افت تولید در ورق سرد در شرایط افزایش تولید خودرو و لوازمخانگی قابلتامل است.
قطع برق میتواند آسیبهای جدی به تولیدکنندگان فولاد وارد کند
اولین و مهمترین آسیب، توقف تولید است. کارخانههای فولاد برای تولید محصولات خود نیاز به انرژی مداوم دارند و هرگونه قطع برق میتواند باعث توقف خطوط تولید شود. این توقفها میتواند هزینههای بالایی برای تولیدکنندگان داشته باشد. توقف تولید نهتنها به کاهش درآمد منجر میشود، بلکه میتواند قراردادهای موجود را نیز تحتتاثیر قرار دهد و موجب از دست رفتن مشتریان شود. دومین آسیب، کاهش کیفیت محصولات است. فرآیند تولید فولاد نیازمند کنترل دقیق دما و فشار است و قطع برق میتواند باعث عدمتعادل در این فرآیندها شود. این عدمتعادل میتواند منجر به تولید محصولات با کیفیت پایینتر و در نتیجه کاهش ارزش آنها در بازار شود. کاهش کیفیت محصولات میتواند به از دست رفتن اعتماد مشتریان و کاهش سهم بازار منجر شود.
سخن پایانی
قطعی برق یک چالش جدی برای صنعت فولاد است که تاثیرات گسترده ای بر تولیدکنندگان و قیمت محصولات فولادی دارد. با توجه به نقش مهم فولاد در صنایع مختلف، توجه به این مسئله و اتخاذ تدابیر مناسب برای کاهش تاثیرات آن از اهمیت بالایی برخوردار است.